Industrial rollers: the backbone of flat-product manufacturing
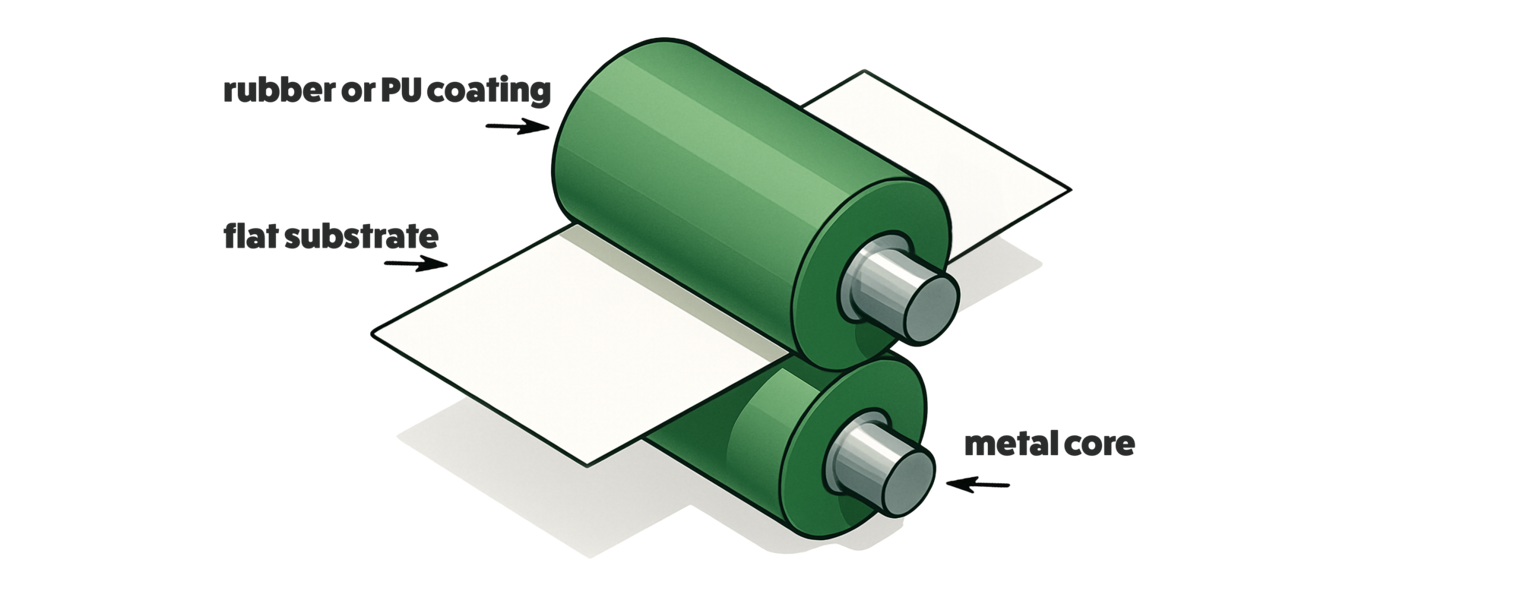
Industrial rollers are the silent workhorses behind the continuous production of all manner of flat substrates, the sheets and films that form so many everyday items we touch. From the sheets of steel used in car parts to the pages of your favorite book, these rolling cylinders make continuous production possible. In a cold-rolling mill, for example, huge slabs of steel pass between two powerful rollers that squeeze them down to exactly the right thickness. In a paper mill, wet pulp moves under rollers that press out water and smooth the surface, turning soggy mash into crisp sheets of paper. Even plastic films (think cling wrap) and laminated packaging travel through rollers that measure out a perfect layer of material, then chill it into form. Textiles, aluminum foil, medical fabrics, …. all these flat products rely on rollers to guide their paths, keep tension steady, and apply just the right pressure so the end result is even, smooth, and free of defects.
What rollers actually do
At first glance, an industrial roller looks like a simple metal tube. But each roller is carefully designed to do a specific job:
- Guiding and tensioning
Imagine running a long ribbon through two paint rollers. If one roller moves faster than the other, the ribbon would wrinkle or break. Rollers match speeds and hold materials tight, preventing snags, tears, and uneven edges as products speed along the line. - Pressing and shaping
Whether you’re smoothing out paper or bonding plastic layers together, rollers press down with controlled force. This “nip” action determines the final thickness and finish (glossy, matte, embossed, or plain) depending on the material and the rollers’ settings. - Coating and metering
In printing and coating, rollers can carry a thin film of ink or glue and deposit it evenly onto the moving web. Think of an anilox roller in a flexographic press: its tiny cells hold a precise amount of ink, so every label or carton looks just right. - Texturing and embossing
A patterned roller can leave a decorative or functional texture on vinyl flooring, wallpaper, or nonwoven fabrics. The engraved design rolls right into the surface in a single pass, saving time and energy. - Heating and cooling
Some rollers have built-in channels for steam, hot water, or chilled fluid. As the material rolls by, it dries, cures, or cools down instantly, no extra machines needed.
Why the coating matters
Underneath the outer layer, every roller has a steel core. But it’s the coating, usually rubber or polyurethane (PU), that touches the product. A soft rubber cover grips delicate paper without tearing it, while a thicker PU coating resists wear when rolling abrasive materials. The thickness and hardness of this coating control how much give the roller has, so it can absorb shocks or deliver precision. In heavy-duty lines, a thicker, tougher cover means fewer breakdowns and longer run times; in gentle processes, a softer cover prevents marks or scratches.
Making the right choice
Choosing the perfect roller is a bit like picking the right shoe: it needs to fit the job. Engineers look at the material’s toughness, the line speed, and the environment (high heat, chemicals, clean-room requirements) to decide on coating type, hardness, thickness, and surface finish. The goal is always the same: keep the line running smoothly, make the product look and perform at its best, and reduce unplanned stops for maintenance.
Conclusion
Industrial rollers may seem simple, but they’re finely tuned tools at the heart of manufacturing. From the steel sheets that build cars to the glossy pages you read, rollers guide, press, coat, and finish flat materials with precision and speed. Next time you unroll aluminum foil or flip through a magazine, take a moment to appreciate the humble roller whose steady spin made it all possible.